Friction: The key to a safe and competent haul road operations
- ADE
- Jul 1, 2017
- 3 min read
The team at ADE pride themselves on being able to offer solutions to the challenges their clients face daily working in the mining and construction industries. Read on to learn more about friction and the important part it plays in safety and operating costs from ADE's Global Sales Manager, Eric Tomicek.
In our day-to-day travels, most of us are fortunate enough to drive on well-designed permanently sealed road surfaces that provide high levels of friction even in wet conditions. Whilst we take extra caution when the roads are wet, for the most part we are still able to maintain safe vehicle operation without substantially reducing the vehicle speed when compared to dry conditions.

It is just not possible for mining operations to have a network of sealed roads as their haul roads are predominantly transient entities. Miners have to make the most of the options they have available to them. This means having to operate vehicles on an unsealed dirt road where friction levels can change dramatically when they are wet. It's a challenge that miners face every day; how do you provide a safe working environment and maintain an efficient and prosperous haul road circuit operation?
Driving light and heavy vehicles on an unsealed road is a difficult task as the drivers have to contend with a range of road conditions; with water just being one of them. To ensure that vehicles are being driven safely to the conditions most operators usually estimate the available friction and then try to ensure that they don't operate a vehicle beyond the limit of control. In a light vehicle, this guessing game can result in a momentary loss of traction or a small slide when we get it wrong, but in a heavy vehicle or large mining dump truck the consequence of a small error can be extremely costly.
Mining supervisors are often tasked with deciding if the haul road conditions are safe for a vehicle to operate on after a rain event or at worst, after a vehicle slide. They are often left questioning if the water trucks are outputting a safe level of water, and, if it rains, when is it safe to return to operation? These decisions have traditionally been made using a combination of experience and feel. Supervisors will often drive the haul roads in their light vehicles, using their senses to feel how the vehicle is reacting to throttle, brake and steering inputs, allowing them to get a 'feel' for the level of friction.
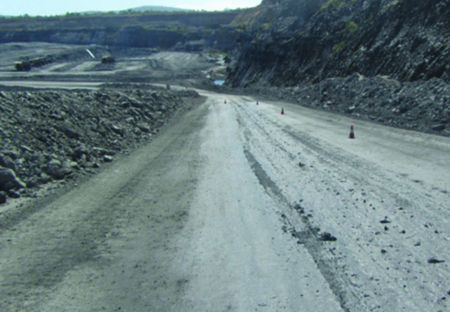
The problem with this approach is that, like opinions, the results are all calibrated differently. Everyone has a differing acceptance level for what may or may not be safe. This wouldn't be so much of a problem if the output of this feeling was solely for their own use. However, these decisions made from gut feel are generally then implemented by someone else who also most likely will have their own, and possibly differing sense of the road conditions . For example, I might be more conservative in my approach than someone who is a world off-road rally champion. Clearly therefore two different decisions about "what is safe" can have possibly hazardous results.
There is however now a better way of making haul road safety decisions with the introduction of quantitative measurement. The Safe Road System, developed by RoadSafety Training Services, is a process and methodology that supports decisions related to road friction and safe vehicle operations. The Safe Road System is now a standard part of the decision making process on many Australian mining operations. ADE is proud to be the only authorised RoadSafety consultant in the world offering training programs and auditing services.
Comments