Q&A: Watering Haul Roads
- ADE
- Oct 21, 2022
- 5 min read
There are different ways to build and operate haul roads on surface mines and many different challenges, but when it comes to haul road dust suppression, the only tried and true method is the humble water truck.
Eric Tomicek ,Global Sales Manager of Australian Diversified Engineering has worked closely with tank manufacturers, OEM’s, mining companies, contractors and rental providers around the globe delivering and supporting water trucks fitted with the industry trusted ADE Spray system.
Eric shares his experience and learnings and what’s coming next.

What’s so important about a water truck?
It’s one of the many unsung heroes on a mine site, sure they don’t dig dirt and they don’t move it, but without them things come to a halt very quick. If a water truck sprays too much water roads become a significant safety hazard ,if they don’t spray enough water the air gets dusty very quickly, for those on the haul road this means loss of visibility almost like driving through heavy fog, and if winds blow the dust outside of the mine there will be unhappy neighbours. It is such a critical thing to get right, there is both safety and economic benefits beyond the water truck itself.
What drove advancements in water truck operations?
A spate of truck slides and vehicle rollovers got the attention of the mine safety authority, the simple reason was that haul roads were being overwatered. The spray controls fitted to these water trucks did not give adequate control over water output and thein-cab controls offered to water truck operators were meaningless.
The challenge is water trucks need to travel at a slow crawl up a ramp spraying at a light sprinkle and then seamlessly transition into a sprint on the flat haul roads pumping tonnes of water per minute, this is a huge variation in water flow and needs a robust control system supported by smart technical design and a very simple and logical user interface.
How did ADE modernise water truck operations?
The short answer is that we learnt about haul road friction from a respected police forensic crash investigator and understood the requirements for haul road watering to maintain safe friction levels, we then designed a water truck control system(ADE Spray)that sprays at a metered rate and can be linked with the results of haul road friction testing. We’ve added customisable settings and spray modes so that the spray system can automatically enforce maximum spray rate limits depending on if it is spraying a flat haul road or a ramp, and we have nice to haves like data logging and third party FMS system integration. We also offer a free iPhone app for haul road friction measurement and we provide the necessary site training.

Is it as simple as upgrading hardware?
No, just like lane keeping and radar guided cruise control on modern cars doesn’t necessarily make safer drivers and roads, upgrading to a modern spray system like ADE Spray still requires training to be rolled out on site and ideally sites should consider updating outdated operating procedures. An online operator training course is one way ADE has made it easier for sites to roll out training, we can also assist with integrating the ADE training into the onsite training management system. Water trucks also work in one of the worst environments on a mine site, every site claims to have the worse water quality, this water wreaks havoc with steel, seals, pumps and electrical connectors. ADE has invested in local product managers and stock to support mining customers when they need it.
A mine site is interested in safety, what do you tell them?
Knowing how much water is being applied to the ground is critical for mine site safety, the metered spray rate to a water truck is like the speedometer to a car, without it we don’t know how fast weare going and therefore cannot implement limits or controls. Having a control system means every water truck can achieve the same outcome and operators can easily communicate what works and doesn’t work.
Getting operators understanding the spray rates is the priority, then if necessary we can set limits as required to enforce safer operations. If safety is an ongoing issue on a site, we recommend supervisors implement ongoing friction testing audits to ensure the spray rates that are being used meet the safety requirements of the mine site, this is also a great opportunity for supervisors to provide feedback to water truck operators. Without friction testing it is the haul truck operators that are the pioneers and unfortunately you can’t see friction, so hopefully it isn’t too slippery the next time they are trying to descend that ramp.
Everyone wants to save money, can a modern water truck do that?
Yes! Because of the safety issues with overwatering, most legacy water trucks are optimised to spray less water at low speed traction critical zones, but this means top end water output is restricted. The ADE Spray system use low flow nozzles for slow speed and high flow nozzles are turned on as speed is increased. Consistent water application is still maintained and now more water is safely being applied to more of the mine.
This could mean parking up a water truck or two because the other three can achieve the same level of dust suppression. Or if you’re struggling with dust control, upgrading your fleet can provide a higher total water output compared to deploying another legacy water truck. Improving haul road conditions can also mean reduced road maintenance, reduced rolling resistance and increased tyre life.

What are some of the bad things you’ve seen... what can miners reading this look out for?
I recall riding shotgun in a water truck prior to submitting a tender, the ramps were spot sprayed and as we drove through the wet spot sections there was wheel spin. This was apparently a common occurrence, even for the ultra-class dump trucks who would occasionally get stuck half way up a ramp. The solution for stuck dump trucks...“just wait for it to dry out” was the reply from my tour guide. The same site also suffered from considerable dust delays and was operating over 10 water trucks.
In the past it was common for water truck operators to take the full blame for any over watering related incident. It then became common to audit water trucks as part of incident investigations to determine water output under various conditions and settings. The overwhelming result was that legacy water trucks were simply designed to overwater and no amount of fiddling with settings by the operator made a difference. It was an eye opener for some sites that realised the responsibility fell on them to provide suitable functioning equipment to their operators.
Autonomous haulage is becoming more prevalent, what does this mean for the water truck?
Autonomous operations require defined parameters, this makes metered spray rates and friction testing critical for deploying autonomous water trucks. The discretion of the water truck operator that was once relied on to determine safe water application rates and reapplication rates will need be managed elsewhere.
I’ll leave that process management decision to the autonomous haulage experts, for the ADE Spray system, we already offer a gateway module that provides real time spray system information and remote control capabilities that can be used by an autonomous system provider to deploy an ADE Spray fitted autonomous water truck.
Read more here: www.amsj.com.au
Australasian Mine Safety Journal: August 2022 Edition
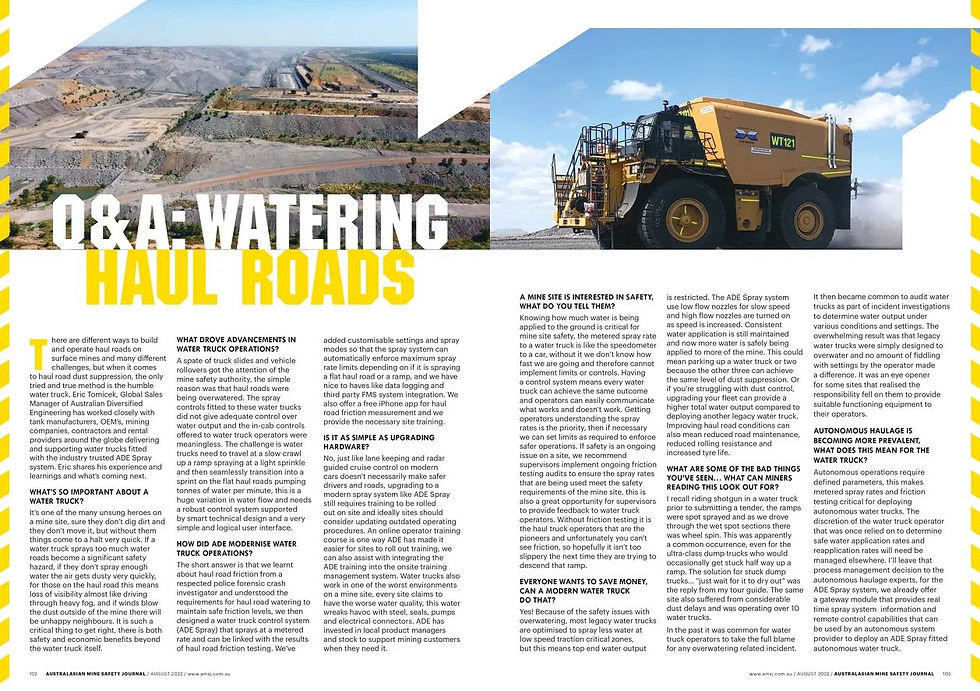
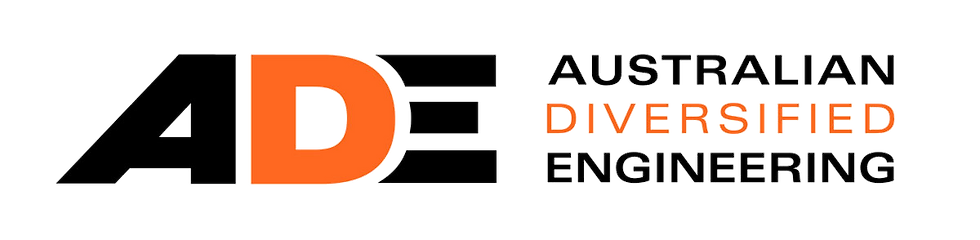
Comentários